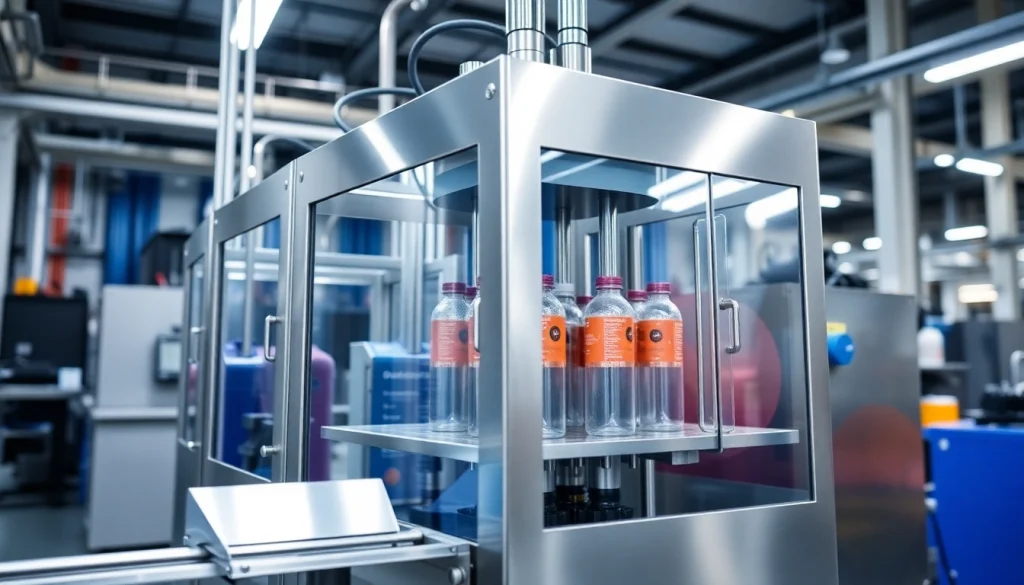
Understanding Filling Machines
In the manufacturing and packaging industries, filling machines play a crucial role in ensuring the efficient and accurate distribution of liquids, powders, and other materials into containers. These machines are vital for businesses looking to streamline their production processes while maintaining quality and compliance. Understanding how filling machines work, the types available, and their applications can significantly impact operational efficiency and product consistency.
What is a Filling Machine?
A filling machine is a device designed to dispense a specific quantity of product into containers such as bottles, jars, and pouches. Customarily seen in food and beverage, pharmaceutical, and cosmetic industries, filling machines reduce human error and boost productivity. They are equipped to handle various materials, from thick pastes to thin liquids, and are essential for businesses aiming to achieve higher throughput rates.
Types of Filling Machines
Filling machines come in various types, each designed to meet the specific needs of different industries. Here are some common types:
- Liquid Filling Machines: Designed for filling liquids, these machines can be further classified into:
- Piston Fillers: Ideal for thick viscous products.
- Gravity Fillers: Suitable for thin and free-flowing liquids.
- Pump Fillers: Used for various liquid viscosities.
- Powder Filling Machines: These systems are designed to fill powders accurately into containers. They often feature auger fillers for precise measurement.
- Quantitative Fillers: Used for products requiring precise weight or volume measurement.
- Automated vs. Manual Machines: Automated machines offer faster throughput and less labor intensity, while manual machines are suitable for lower volume production.
Key Applications in Various Industries
Filling machines are used across numerous sectors, each with distinct requirements:
- Food and Beverage: Filling machines in this sector help package products such as sauces, juices, and dairy items, ensuring hygiene and compliance with food safety standards.
- Pharmaceuticals: These machines require strict adherence to regulations, as they are used for filling medications, both in liquid and tablet forms.
- Cosmetics: From lotions to creams, filling machines in cosmetics must handle various viscosities while maintaining product integrity and precision.
- Chemicals: They are often utilized for packaging hazardous substances, requiring additional safety features and compliance checks.
Choosing the Right Filling Machine
When it comes to selecting a filling machine, the process can be overwhelming due to the variety of options available. However, understanding your specific needs can facilitate a sound decision.
Factors to Consider for Your Business
Several key factors should be evaluated before investing in a filling machine:
- Product Type: Assess the physical and chemical properties of the product, including viscosity, pH, and whether it’s hazardous.
- Container Specifications: Evaluate the type, shape, and size of containers to ensure compatibility with the filling machine.
- Production Volume: Consider your production capacity. Automated machines are ideal for high volumes.
- Budget: Establish a budget that encompasses the cost of the machine, installation, and potential maintenance expenses.
- Regulatory Compliance: Ensure that the machines meet the necessary industry regulations and standards.
Common Mistakes to Avoid
Businesses often overlook critical details that can lead to costly mistakes:
- Choosing the wrong type of filling machine that doesn’t suit product specifications.
- Underestimating the importance of post-purchase support and maintenance agreements.
- Failing to conduct thorough testing for compatibility with existing production lines.
Consulting with a Filling Machine Supplier
Consulting with a Filling Machine Supplier is essential. They can provide insights based on their expertise, helping you choose the best machine tailored to your business needs. A good supplier will also assist with installation, training, and ongoing support, ensuring the machine operates at peak efficiency.
Benefits of Automated Filling Systems
Incorporating automated filling systems into production lines brings numerous advantages that can significantly impact your business operations.
Increased Efficiency and Productivity
Automated filling machines are designed to operate at high speeds with minimal downtime, enabling manufacturers to achieve higher production rates compared to manual filling. Efficient design leads to optimized workflow, maximizing output.
Cost Savings on Labor and Materials
Using automated systems reduces the need for extensive manual labor, which translates to lower labor costs. Additionally, these systems reduce material waste through accurate measurements, ultimately saving money over time!
Improved Accuracy and Consistency
Accuracy in filling is vital, especially in regulated industries like pharmaceuticals. Automated filling machines minimize human error, ensuring that each container is filled to the designated specification consistently.
Maintenance and Support for Filling Machines
Proper maintenance of filling machines is crucial for ensuring long-term reliability and efficiency.
Routine Maintenance Best Practices
Establishing a maintenance schedule is essential to prolong the lifespan of your filling equipment. Regular checks and maintenance activities include:
- Daily inspections to ensure cleanliness and functionality.
- Regular calibration for accuracy in measurements.
- Monitoring for wear and tear on parts, replacing them as necessary.
Finding Reliable Support Services
Partnering with a filling machine supplier that offers reliable support services is essential. Ensure that they provide accessible customer service and technical assistance when needed, helping to address any concerns or repairs promptly.
Extending the Life of Your Equipment
To further extend the life of your filling machines, consider investing in high-quality components and upgrades as technology advances. Regular training for your staff on proper operational procedures can also enhance machine longevity.
Case Studies and Success Stories
Real-world applications and success stories can provide valuable insights into the impact of the optimal filling machine selection.
Business Growth with the Right Machinery
A case study involving a beverage company revealed that upgrading to an automated filling system increased their production capacity by 50%, leading to significantly higher revenues without substantial increases in labor costs.
Innovative Solutions by Leading Suppliers
Several leading suppliers have developed custom solutions that address specific industry challenges. For example, a cosmetics manufacturer faced issues with batch inconsistency, which was solved through a specialized filling machine tailored for high-viscosity materials.
Customer Testimonials and Feedback
Gathering customer testimonials can provide insights into the effectiveness of a product. For instance, an industrial client highlighted how their new filling system not only improved efficiency but also significantly reduced downtime, allowing them to meet tighter deadlines.