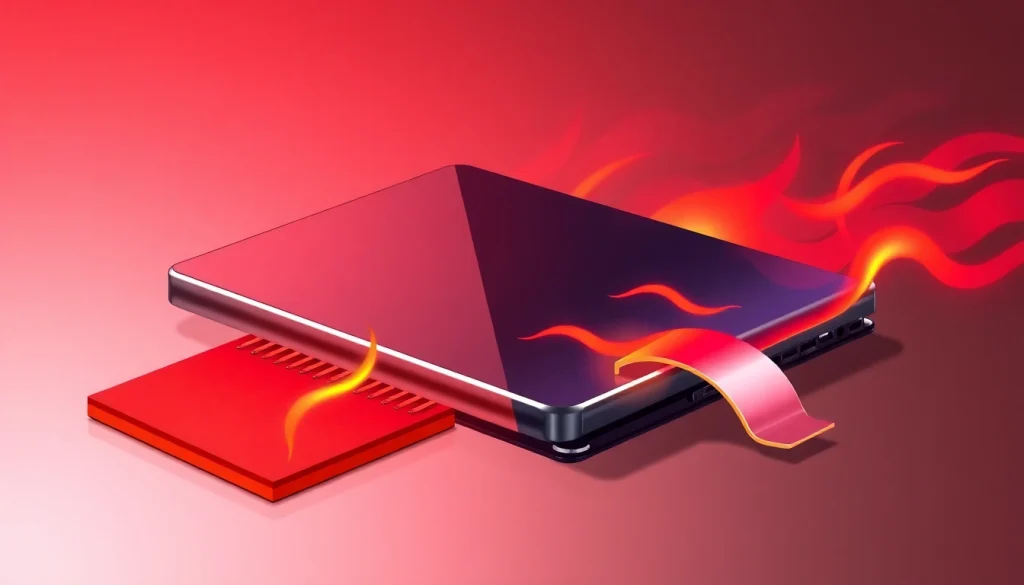
Understanding Thermal Management Materials
In the rapidly evolving world of electronics, managing heat is a critical component in the design and operation of devices. Thermal management materials play an essential role in dissipating heat generated by electronic components, ensuring their longevity and performance. Thermal management materials encompass a wide range of substances utilized in various applications, including thermal interface materials, gap fillers, and phase change materials. This article provides comprehensive insights into these materials, their types, applications, selection criteria, best practices for installation, and future trends within the sector.
What are Thermal Management Materials?
Thermal management materials are substances designed to regulate heat flow between components in electronic systems. The demand for efficiency and performance in electronics has surged, primarily due to high-frequency operations and miniaturized components, necessitating effective heat dissipation. These materials can be categorized based on their function, thermal conductivity, and application environments, each serving a specific purpose in thermal management strategies.
The Importance of Effective Heat Dissipation
Effective heat dissipation is vital in preventing overheating, which can lead to device failure, inefficient performance, and reduced lifespan. As electronic devices become more compact, the heat generated per unit area increases, intensifying the need for robust thermal management solutions. Thermal failure often manifests as lower reliability of your devices, which can severely affect the end-user experience and may lead to costly repairs or replacements. By utilizing thermal management materials, manufacturers can enhance thermal conductivity, maintain optimal operating temperatures, and ensure component integrity.
Applications Across Industries
Thermal management materials find applications across a myriad of industries, including consumer electronics, automotive, aerospace, and renewable energy. For instance:
- Consumer Electronics: In devices such as smartphones, laptops, and gaming consoles, managing heat is crucial for performance and user comfort.
- Automotive: In electric vehicles, sophisticated thermal management systems are vital to maintain battery performance and safety.
- Aerospace: Thermal materials are used to protect sensitive equipment from the extreme temperatures of high-altitude flight.
- Renewable Energy: Solar panels and wind turbines utilize thermal materials to enhance energy conversion efficiency and manage operational heat.
Types of Thermal Management Materials
Thermal Interface Materials (TIMs)
Thermal Interface Materials, or TIMs, are substances used to improve thermal energy transfer between two surfaces. They are typically placed between heat-producing elements, such as CPU chips, and heat sinks or cooling systems. Common types of TIMs include:
- Thermal Greases: These are viscous compounds that fill microscopic gaps between surfaces to improve thermal contact
- Thermal Pads: Soft pads that provide cushioning while conducting heat away from sensitive electronic components.
- Phase Change Materials (PCMs): These materials change their physical state in response to temperature changes, absorbing excessive heat.
Phase Change Materials (PCMs)
Phase Change Materials feature unique properties that allow them to absorb and release heat during phase transitions. Commonly used in applications requiring temperature stability, PCMs are found in:
- Electronics: Used in devices to maintain temperature during peak operational phases.
- Building Materials: Incorporated into walls to regulate indoor temperatures, reducing energy consumption.
As modern electronics evolve, the reliance on PCMs continues to grow due to their thermal regulation capabilities.
Thermal Pads and Tapes
These are versatile solutions for heat transfer applications. Thermal pads offer cushioning along with thermal conductivity, making them suitable for uneven surfaces. Thermal tapes serve as adhesive and thermal conductors, allowing for simple installation and reliability in securing components.
Choosing the Right Thermal Management Materials
Key Factors to Consider
When selecting thermal management materials, several crucial factors come into play:
- Thermal Conductivity: This is the primary metric indicating how effectively a material can transfer heat. Higher thermal conductivity values are generally preferable.
- Dielectric Strength: Important for electrical insulation properties, particularly in electronic applications.
- Thickness and Compressibility: Considerations for ensuring adequate contact and filling voids between mating surfaces.
- Operating Temperature Range: The material should withstand the temperatures expected in the application without degradation.
Performance Metrics and Testing
Performance metrics for thermal management materials often include thermal resistance, thermal impedance, and thermal conductivity ratios. Testing these materials is critical before implementation and typically involves:
- Application Testing: Real-world applications to validate efficiency under expected operational conditions.
- Standardized Tests: Lab testing according to established standards that provide reliable performance benchmarks.
Application-Specific Recommendations
Each application may have specific requirements for thermal management materials. Hence, fine-tuning material selection based on the application is pivotal. For sensitive electronics, softer pads might provide better contact, while rigid materials would suit heavier equipment requiring robust thermal pathways.
Installation and Implementation Best Practices
Preparing Surfaces for Optimal Adhesion
Successful installation of thermal management materials hinges largely on surface preparation. Here are key steps:
- Ensure that surfaces are clean, dry, and free of contaminants.
- Utilize isopropyl alcohol or similar cleaning agents to remove oils or residues.
- Roughen surfaces when appropriate, as this can enhance adhesion.
Common Installation Mistakes to Avoid
Some frequent missteps during installation can hinder performance:
- Insufficient Application: Utilizing too little material can leave voids that degrade thermal transfer.
- Over-compression: Excessive pressure can squeeze out effective materials and create air pockets.
- Incorrect Material Type: Using a material not suited for the temperature or application can lead to premature failure.
Maintenance Tips for Longevity
To ensure the effectiveness of thermal management materials over time, consider the following maintenance tips:
- Regularly inspect systems for signs of wear or thermal degradation.
- Replace materials that show signs of damage, such as cracking or discoloration.
- Monitor operating temperatures to identify potential issues before failures occur.
Future Trends in Thermal Management Materials
Innovations in Material Science
The field of thermal management materials is witnessing constant innovation. Advanced composites and nanomaterials promise higher thermal conductivities and reduced weights. Research into hybrid materials that can adapt their thermal properties dynamically is also underway, potentially revolutionizing how heat is managed in sensitive applications.
Impact of Technology Advancements
As technology progresses, the requirements placed on thermal management systems will become more stringent. Electronics will demand higher heat density and compact designs, necessitating ongoing advancements in thermal materials. This environment encourages the exploration of materials that can operate efficiently under increasingly challenging conditions.
Sustainability in Thermal Management Solutions
With a growing emphasis on sustainability and environmental impact, the development of green thermal management materials is becoming essential. Research is focused on creating materials with lower carbon footprints and longer lifespans, ensuring that the material lifecycle aligns with overall sustainability goals across industries.