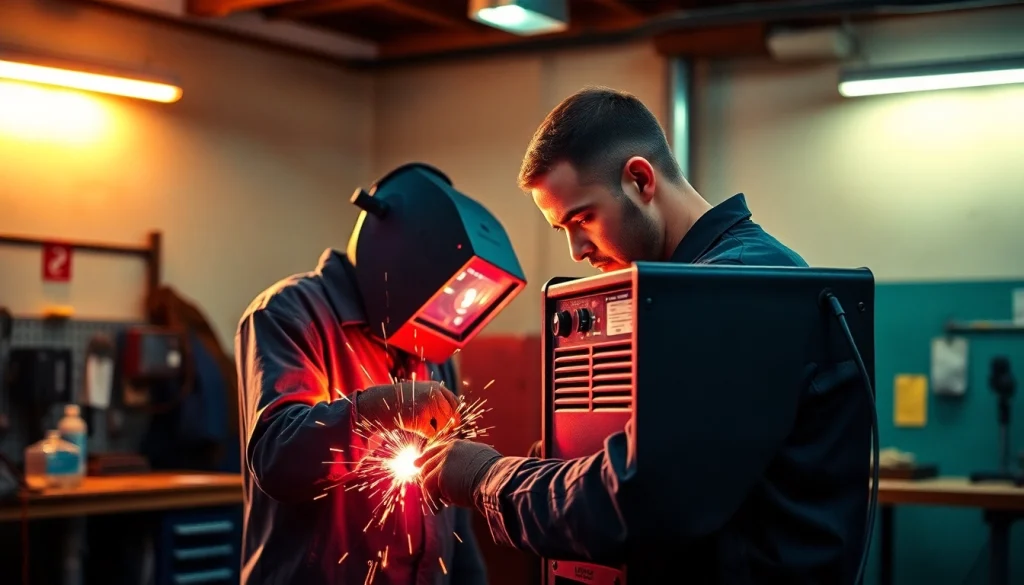
Understanding the Unimig Tig Welder
Welding is a vital skill across various industries, from manufacturing to automotive and beyond. Within the diverse world of welding techniques, TIG welding, also known as gas tungsten arc welding (GTAW), stands out for its precision and versatility. A significant player in this field is the unimig tig welder, well-regarded for its high-quality construction and performance capabilities. This article will guide you through essential information related to Unimig TIG welders, helping you understand their advantages, models, setup, techniques, and maintenance for maximizing your welding projects.
What is TIG Welding?
TIG welding is a process that utilizes a non-consumable tungsten electrode to produce the weld. In this technique, a shielding gas—most commonly argon—is used to protect the weld zone from oxidation and contamination. This method is particularly beneficial for welding thin sections of stainless steel and non-ferrous metals such as aluminum and copper. The process offers great control over the weld, making it ideal for high-quality, precision applications.
Benefits of Unimig TIG Welders
Unimig TIG welders bring numerous advantages to both hobbyists and professionals. Below are some highlighted benefits:
- Versatility: Unimig models typically support AC and DC welding, allowing them to handle a wide range of materials.
- Precision: The TIG welding process allows the welder to deliver accurate and clean welds, making it ideal for critical applications.
- User-friendly: Many Unimig models come equipped with intuitive controls and settings, making them accessible for beginners.
- Durability: Built with robust materials, Unimig TIG welders can withstand demanding working conditions and deliver long-lasting performance.
- Advanced Features: Features such as high-frequency start, pulse welding capability, and synergic control settings enhance usability.
Overview of Popular Unimig Models
Among the most sought-after Unimig TIG welders are the Viper and Razor series. Here’s a closer look at some of the standout models:
- Viper 185: A compact and lightweight machine ideal for portable applications. It offers multi-process functionality for MIG, TIG, and stick welding.
- Razor 200 AC/DC: Known for its professional capabilities, the Razor 200 provides robust performance across various welding applications, including aluminum and stainless steel.
- VIPER TIG 180 AC/DC Mk II: Designed for versatile applications, it features high-frequency arc initiation and excellent arc stability.
Choosing the Right Unimig Model For Your Needs
When selecting the right Unimig TIG welder, several factors must be considered. Each model has unique features designed to meet different welding requirements.
Comparing Viper vs Razor Series
The Viper and Razor series offer distinct advantages depending on user needs:
- Viper Series: Aimed at general users and DIY enthusiasts, the Viper series operates with easy-to-understand controls and offers capabilities for a variety of welding projects.
- Razor Series: Targeted toward professionals, offering additional features suited for demanding industrial applications, higher power ratings, and enhanced functionality for precision welding.
Key Features to Look For
When investing in a TIG welder, consider the following essential features:
- AC/DC Capability: Enables welding of both ferrous and non-ferrous metals.
- Pulsing Function: Provides greater control over heat input, which is critical for working with thin materials.
- Foot Pedal Control: Allows for better amperage adjustments during the welding process, enhancing precision.
- Cooling System: An efficient cooling system prevents the welder from overheating, ensuring longevity.
- Portability: Lightweight and compact designs are crucial for mobile applications.
Price vs Performance: Making the Right Choice
While price is a significant consideration when purchasing a Unimig TIG welder, it is essential to evaluate it in conjunction with performance. Investing in a more expensive model that offers superior features and durability can save you money in the long run by reducing repair needs. Assess your specific applications, welding materials, and expected hours of use to determine the best value for your budget.
Setting Up Your Unimig Tig Welder
Setting up your Unimig TIG welder correctly is crucial for achieving optimal welding performance and ensuring safety. Here, we’ll explore the essential steps and tools needed for setup.
Essential Tools and Accessories
Before starting, gather the following tools and accessories:
- TIG welding torch with appropriate tungsten electrode
- Argon gas cylinder and regulator
- Welding gloves and helmet
- Safety glasses and protective clothing
- Welding filler rods suitable for your metal types
- Ground clamp
Step-by-step Setup Guide
Follow these general steps to set up your Unimig TIG welder:
- Connect the Gas Cylinder: Securely attach the regulator to your argon gas cylinder and connect it to the welder.
- Install the Tungsten Electrode: Insert the appropriate tungsten electrode into the TIG torch.
- Attach the Filler Rod Holder: If using a filler rod, ensure it is positioned within easy reach of the torch.
- Connect the Ground Clamp: Attach the ground clamp securely to the workpiece to ensure a good electrical connection.
- Set the Parameters: Adjust the welder settings according to the material type and thickness.
- Test the Gas Flow: Open the gas valve on the regulator and verify that gas flows from the torch.
Troubleshooting Common Issues
Even with proper setup, issues may arise. Here are common troubleshooting tips for TIG welding with Unimig machines:
- Weak Arc or No Arc: Ensure the machine is properly grounded and check the settings. Inspect the gas flow and replace the tungsten electrode if necessary.
- Inconsistent Welds: Evaluate your welding speed and technique. Ensure the tungsten is clean and correctly shaped.
- Gas Contamination: Check for leaks in the gas lines, ensure the proper type of gas is being used, and replace hoses if they appear damaged.
TIG Welding Techniques with Unimig Welders
Mastering TIG welding techniques is essential for ensuring high-quality welds. Below are essential techniques and practices to enhance your welding results.
Mastering Penetration and Heat Control
Effective penetration and heat control are critical in achieving strong welds. Here are some techniques to enhance these aspects:
- Proper Amperage Settings: Adjust the amperage based on the material thickness for optimal penetration without warping.
- Travel Speed: Control your travel speed to maintain appropriate heat input and prevent overheating.
- Tungsten Positioning: Angle the tungsten electrode correctly towards the workpiece to focus the weld pool effectively.
Special Techniques for Different Materials
Diverse materials require unique techniques. Here’s a breakdown:
- Aluminum: Use AC polarity for aluminum welding and consider using a larger tungsten electrode size for improved heat management.
- Stainless Steel: Welding with DC straight polarity is ideal; ensure proper cleaning of surfaces beforehand.
- Copper: Consult specific guidelines for copper alloys and consider preheating thicker sections.
Safety Practices for TIG Welding
Safety must always come first in welding operations. Utilize the following practices:
- Always wear appropriate personal protective equipment (PPE), including gloves, helmets, and goggles.
- Perform welding in well-ventilated areas to minimize exposure to harmful fumes.
- Keep a fire extinguisher handy in case of emergencies.
- Learn proper emergency procedures for your workspace.
Maintaining Your Unimig Tig Welder
Proper maintenance ensures longevity and performance of your Unimig TIG welder. Here are best practices for upkeep:
Regular Maintenance Tips
Implement the following maintenance routines:
- Regularly inspect cables and connections for wear and replace them as necessary.
- Clean the outside of the welder and ensure the cooling vents are free from debris.
- Check and replace the gas filter on a schedule to ensure consistent gas flow.
- Examine and clean the torch and electrode regularly, replacing when needed.
When to Seek Professional Assistance
If you experience persistent issues that you cannot resolve through basic troubleshooting and maintenance, it may be time to consult a professional technician. Signs that professional repair may be needed include:
- Strange noises or sparks during operation.
- Lack of power despite correct setup and settings.
- Repeated electrical issues or burnout of components.
Enhancing Longevity and Performance
To ensure optimal performance over the lifespan of your Unimig TIG welder, consider the following tips:
- Store the welder in a clean, dry environment when not in use.
- Invest in quality accessories that complement your model and avoid using generic or low-quality parts.
- Adhere to the manufacturer’s guidelines for maintenance schedules and usage.