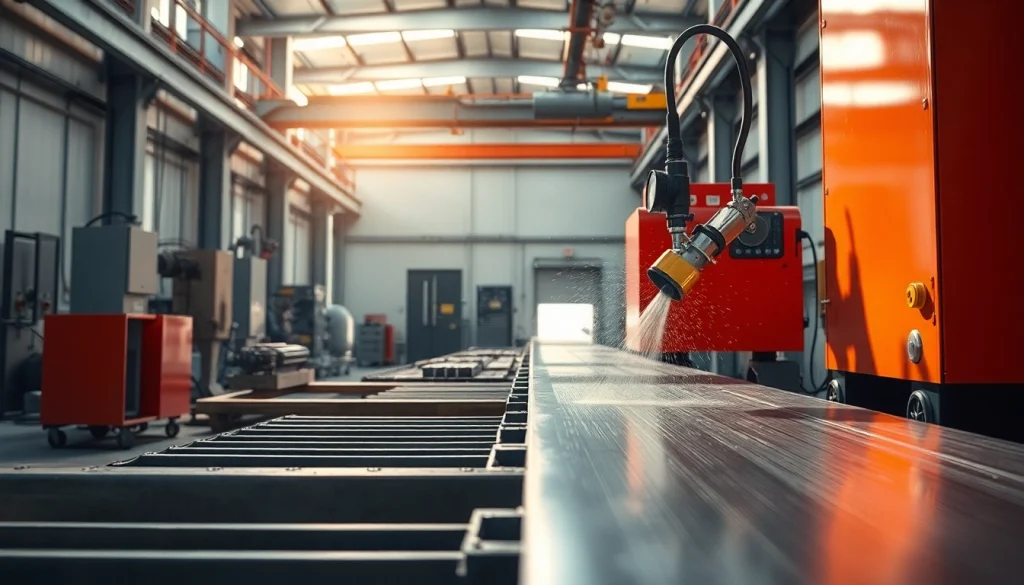
Introduction to EP Coating
Electrophoretic coating, commonly known as EP coating or e-coating, is a revolutionary surface treatment technique that has gained significant attention in various industries. This process is renowned for its ability to provide a durable protective layer to a wide range of metal components, thereby enhancing their longevity and resistance to corrosion. Additionally, the environmental benefits associated with EP coating make it a popular choice among manufacturers seeking sustainable solutions. For insights into how EP coating can be integrated into your manufacturing process, ep coating is an essential component to explore.
What is EP Coating?
Electrophoretic coating is a method of applying a paint layer to a conductive surface through the process of electrolysis. In this process, particles of paint are suspended in a liquid and deposited onto the surface of a substrate when an electric current is applied. The primary objective is to achieve a uniform coating that adheres well to the substrate. EP coating is highly versatile and can be applied to various metals, including steel, aluminum, and magnesium, among others.
History and Development of Electrophoretic Coating
The roots of electrophoretic coating date back to the early 20th century when the concept of using electric fields to deposit particles was first explored. Initially, the technique was primarily used in laboratory settings. However, the automotive industry in the 1960s began to adopt e-coating for its advantages in corrosion resistance. Over the decades, continued advancements in chemical formulations and technological processes have led to the widespread application of EP coating in various industries, including electronics, aerospace, and consumer goods.
The Importance of Corrosion Resistance in EP Coating
Corrosion resistance is a critical factor in the longevity and performance of metal components. EP coatings form a protective layer that prevents moisture and chemicals from reaching the metal surface. Tests have shown that properly applied EP coatings can significantly extend the service life of components by inhibiting rust and degradation.
The EP Coating Process Explained
Step-by-Step Guide to Electrophoretic Coating
The EP coating process involves several crucial steps:
- Preparation: The substrate surface undergoes thorough cleaning to remove contaminants such as grease, dirt, and oxides. This step is critical as any residue can affect the quality of the coating.
- Electrical Setup: The substrate is connected to a power supply and submerged in a tank filled with the paint solution.
- Electrolysis: Upon applying the electric current, paint particles migrate towards the substrate, adhering to its surface, resulting in an even coating.
- Curing: After the coating process, the parts are usually cured in an oven to harden the coated layer, enhancing durability and adhesion.
Materials Required for Effective EP Coating
Successful EP coating necessitates specific materials and equipment:
- Chemical Bath: A suitable paint formulation mixed in water; the chemicals must be compatible and designed for the given substrate.
- Power Supply: An adjustable power supply to control the voltage during the electrolysis process.
- Tank: A non-conductive tank to hold the painting solution.
- Substrate Preparation Tools: Equipment for cleaning surfaces, including pressure washers and ultrasonic cleaners.
Common Challenges in the Coating Process
Despite its advantages, the EP coating process can encounter several challenges:
- Surface Preparation: Inadequate cleaning can lead to poor adhesion, resulting in coating defects.
- Pit Formation: If the coating is too thick or uneven, defects like pits may form.
- Curing Conditions: Insufficient curing time can lead to a soft and less durable finish.
Addressing these challenges involves rigorous quality control during each stage of the process. Periodically testing the coating for thickness and adherence can mitigate such issues.
Applications of EP Coating Across Industries
Automotive Industry and the Use of EP Coating
The automotive industry is one of the largest users of EP coating due to its effectiveness in protecting car parts from environmental damage. Components such as chassis, body panels, and suspension parts are often coated to ensure longevity and aesthetics. The ability to apply a uniform coating to complex geometries makes e-coat particularly valuable in automotive manufacturing.
Consumer Products Benefiting from EP Coating
EP coating is also prevalent in various consumer goods. The application is especially common in electronics, where durable coatings protect parts from moisture and dust, thereby enhancing product life. Appliances, tools, and furniture often employ electrophoretic coatings for protection and improved aesthetics.
Electrophoretic Coating in Heavy Industry
Heavy industry applications extend to construction equipment, agricultural machinery, and oil rigs, where components are exposed to extreme elements. EP coatings provide the necessary corrosion resistance that ensures these components survive harsh conditions. Additionally, the coatings are chemically resistant, capable of withstanding exposure to fuels, oils, and other corrosive substances commonly found in heavy industries.
EP Coating vs Other Coating Techniques
Electrophoretic Coating vs Powder Coating
While both electrophoretic coating and powder coating serve similar purposes, they have distinct differences. EP coating is typically applied in a liquid state and requires curing, which can lead to variable thickness and application nuances. In contrast, powder coating is a dry application that is electrostatically charged and then cured. This usually results in a thicker coat, but the application process can be less uniform on complex shapes.
Advantages of Using EP Coating Over Anodizing
Anodizing is a common alternative used for aluminum components. While both processes create a protective layer, EP coating is often more versatile in terms of color and finish options. Additionally, EP-coated parts can exhibit superior corrosion resistance compared to anodized layers, particularly in aggressive environments.
Comparative Cost Analysis of Coating Methods
When considering costs, the choice between EP coating and other methods such as powder coating or anodizing depends on several factors, including the scale of production, the type of materials used, and the desired finish. Typically, EP coatings can offer cost-effective solutions for mass production due to their efficiency and the minimal waste generated in the process.
Future of EP Coating Technology
Emerging Trends and Innovations in EP Coating
The future of EP coating technology looks promising, with ongoing research focused on improving coating formulations and application processes. Innovations such as automated systems for real-time monitoring of coating thickness and properties are becoming prevalent, enhancing quality control during production.
Environmental Considerations in Coating Technology
As industries strive for more sustainable practices, EP coating presents an environmentally friendly option. The process generates lower volatile organic compounds (VOCs) compared to traditional solvent-based methods, making it a more sustainable alternative. Manufacturers are continually developing eco-friendly paint formulations that further reduce environmental impact.
The Role of EP Coating in Sustainable Practices
EP coating plays a significant role in sustainable manufacturing by extending the lifespan of metal components, thereby reducing waste and the need for frequent replacements. Additionally, as industries shift towards greener production methods, the demand for such efficient coating solutions is likely to increase.