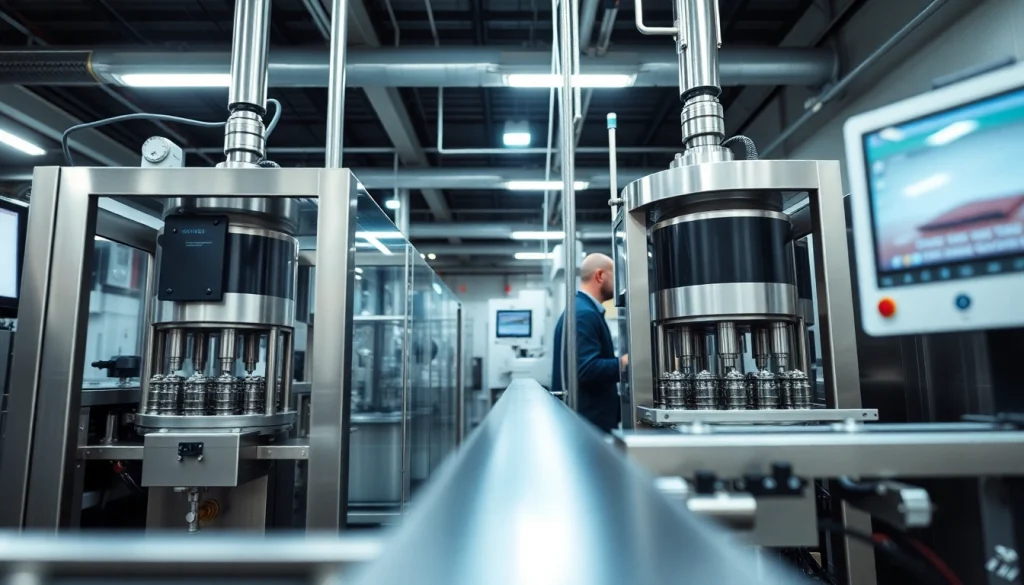
Understanding Filling Machines
What is a Filling Machine?
A filling machine is an essential piece of equipment in the manufacturing and packaging industry. It is meticulously engineered to dispense precise amounts of liquid or viscous products into containers, ensuring consistency and accuracy. These machines are vital across various sectors, including food and beverage, pharmaceuticals, cosmetics, and chemicals. Filling Machine Supplier plays a crucial role in equipping businesses with the right machinery tailored to their specific needs.
Types of Filling Machines
Filling machines come in several types, each designed for different applications and products. Understanding these variations helps businesses choose the right type for their specific requirements.
1. Manual Filling Machines
Manual filling machines are typically operated by hand. They are suitable for low-volume production and are often used by small businesses or in environments where simplicity is key. Operators fill containers using a lever or pump mechanism, making them cost-effective solutions for smaller operations.
2. Semi-Automatic Filling Machines
Semi-automatic machines require some manual input but automate part of the filling process. These systems can significantly increase production speed and accuracy compared to manual machines while still being manageable for operators.
3. Fully Automatic Filling Machines
Fully automatic filling machines are designed for high-volume production environments. They can process bottles or containers without the need for manual intervention, providing consistent filling rates and reducing labor costs. These machines integrate advanced technology to ensure precise filling and can be customized to handle various products, including liquids, gels, and creams.
4. Piston Filling Machines
Piston filling machines use a piston mechanism to dispense liquid products. This type is popular for dense or viscous fluids due to its capability to handle thicker substances effectively.
5. Gravity Filling Machines
Gravity filling machines dispense liquids by utilizing gravity and the principles of fluid dynamics. This type is best suited for thin liquids and operates relying on gravity to move the product from the container to the bottle.
6. Pump Filling Machines
These machines utilize positive displacement pumps to push liquids into containers. They are ideal for products with varying viscosity levels, making them versatile for different applications.
Applications of Filling Machines
Filling machines are indispensable across various industries, each leveraging this technology to enhance productivity, maintain product integrity, and ensure regulatory compliance. Here are some notable applications:
Food and Beverage Industry
In the food and beverage sector, filling machines are crucial for efficiently packaging liquids such as juices, soft drinks, sauces, and oils in bottles or cartons. Ensuring hygiene and minimizing product waste are paramount in this industry.
Pharmaceutical Industry
The pharmaceutical industry relies on filling machines to package drugs and liquid medicines accurately. Precision in dosing and contamination control is critical, and manufacturers often use high-tech machinery to meet these standards.
Cosmetics and Personal Care
Filling machines in the cosmetics sector are used for a diverse range of products including lotions, creams, and oils. These machines often require customization to ensure precise filling without damaging the products.
Chemical Industry
In the chemical industry, filling machines must handle corrosive and hazardous materials. Thus, the technology used often incorporates robust materials and safety features to prevent leaks and ensure operator safety.
Selecting the Right Filling Machine Supplier
Key Qualities of a Reliable Supplier
Choosing the right filling machine supplier can highly impact your operational efficiency and product quality. Below are some critical qualities to look for:
1. Experience and Expertise
It is advisable to work with suppliers who have extensive industry experience and knowledge. This ensures that they understand the specific requirements of different sectors and can provide expert guidance.
2. Range of Products
A supplier offering a comprehensive range of machines can meet various operational needs and provide options that best fit your requirements.
3. Customer Support and Service
Effective after-sales service is vital, as machinery downtime can lead to significant losses. Look for suppliers that offer prompt customer support, including installation, training, and maintenance services.
4. Customization Capabilities
As businesses often have specific needs, suppliers that provide customizable machinery can offer solutions tailored to your operational requirements.
Questions to Ask Potential Suppliers
When engaging with potential suppliers, asking the right questions can help you gauge their suitability:
1. What is your experience in our industry?
Explore how long they have been working with clients in your specific sector and whether they understand its unique challenges.
2. Can you provide references or case studies?
Request references to validate their claims and learn from the experiences of other clients.
3. What warranties and service agreements do you offer?
Understanding the support you will receive post-purchase is crucial for long-term satisfaction.
Evaluating Supplier Credentials
Beyond the initial interactions, conduct further evaluations of potential suppliers:
1. Certifications and Compliance
Ensure the supplier’s products comply with industry standards and regulatory requirements. Certifications like ISO, CE, or FDA approval can indicate reliability.
2. Innovation and Technology
Investigate the supplier’s commitment to innovation. A supplier that invests in new technologies is likely to offer more reliable and efficient solutions.
3. Financial Stability
Assess the financial health of the supplier to ensure they can sustain their operations and support their clients over time.
Innovative Technologies in Filling Machines
Automated Filling Solutions
Automation is a significant trend in manufacturing, and filling machines have embraced advanced technologies to enhance productivity. Automated systems can run continuously, accurately measuring and filling products while minimizing waste.
Customizable Equipment Options
Modern filling machines often come with customizable options tailored for unique applications. This flexibility allows manufacturers to adapt to changing needs and optimize production lines.
Integration with Other Packaging Systems
The ability to integrate filling machines with other packaging equipment, such as labeling and capping machines, creates streamlined workflows, reduces manual handling, and minimizes errors across production lines.
Cost Considerations for Filling Machines
Factors Influencing Machine Costs
When budgeting for a filling machine, several factors can influence the overall cost:
1. Type of Machine
The filling machine type directly affects costs; automated systems are more expensive than manual machines but offer efficiencies that can justify their price.
2. Capacity
The required filling capacity and speed vary per business. Higher-capacity machines often command higher prices but can yield better long-term productivity.
3. Custom Features
Customization options such as additional features or specialized nozzles can influence costs. Be clear on your needs to avoid overspending on unnecessary features.
Long-Term Value of Quality Machines
Investing in high-quality filling machines often leads to long-term savings. Advanced designs enhance efficiency, reduce downtime, and lower the risk of costly errors, making them a worthwhile investment.
Budgeting for Equipment Purchase
Determine a clear budget for purchasing a filling machine. Consider not only the initial investment but also maintenance costs, potential repairs, and upgrades. Evaluate the return on investment (ROI) by analyzing expected production increases and cost savings.
Best Practices for Operating Filling Machines
Maintenance Tips for Longevity
Maximizing the lifespan of your filling machines requires proactive maintenance:
1. Regular Inspections
Schedule regular inspections to identify wear and tear before they lead to significant issues. Look for signs of wear on hoses, pumps, and valves.
2. Lubrication and Cleaning
Keep the machinery clean and properly lubricated, which prevents malfunctions and enhances operational efficiency.
3. Staff Training
Ensure operators are well-trained in both operation and maintenance. Proper training decreases errors and improves production output.
Safety Protocols in Operation
Safety in operation cannot be overstated. Implement safety protocols to minimize risks:
1. Personal Protective Equipment (PPE)
Ensure employees wear appropriate PPE, such as gloves and goggles, especially when handling chemicals.
2. Emergency Procedures
Establish clear emergency procedures and conduct regular drills to prepare for potential malfunctions or accidents.
Training Staff on Equipment Use
Regular training sessions for staff on the operation and potential troubleshooting of filling machines ensure that everyone understands how to use the equipment safely and effectively. Use hands-on training that allows operators to practice while being guided by a knowledgeable supervisor.